First-time fix rate (FTF) is more than a metricāitās a pivotal measure of business performance. Your FTF rates affect customer satisfaction, operational efficiency, and long-term financial value. A high FTF rate can save businesses significant costs while creating lasting customer loyalty. When technicians solve problems in a single visit, they deliver an exceptional experience that builds trust and strengthens your market position.
But meeting this expectation is no easy feat. Todayās service organizations face growing inventory challenges: customers expect instant results, while businesses contend with complex service demands, rising operational costs, and ambitious sustainability targets, all of which directly affect FTF rates. Each repeat service call not only drives up operating expenses but also adds to your carbon footprint, amplifying the urgency for improvement.
Forward-thinking companies are rising above these challenges by embracing predictive inventory management solutions that bridge gaps and streamline processes. With AI in supply chain management, they ensure technicians arrive equipped with the right parts and expertise, enabling seamless supply chain optimization.
The results speak for themselves: reduced costs, stronger customer loyalty, accelerated growth, and a significant reduction in environmental impact.
The Roadblocks to First-Time Fix
Despite the clear benefits of FTF, businesses today struggle to consistently achieve this goal, due to:
Inventory Complexity
Global Service Supply Chains are becoming increasingly complicated due to escalating part variations, ambitious sustainability targets, and availability challenges, all of which impact service parts management. Effectively managing this complexity is essential for ensuring technicians have the right parts on hand to resolve issues the first time.
Technician Skill Gaps
As the āsilver tsunamiā of retiring technicians sweeps through the workforce, businesses are left grappling with a significant skills gap. At the same time, product complexity is increasing, making it harder for new technicians to succeed without proper support.
Data Fragmentation
Disjointed systems and siloed data create blind spots for technicians, highlighting the need for integrated inventory management software. Without real-time data, diagnostics become guesswork, leading to repeated visits and wasted resources.
Reactive Service Models
Organizations stuck in a reactive loop miss out on the AI-powered supply chain capabilities that can prevent disruptions. This approach not only increases downtime but also frustrates customers who expect seamless service.
Cost and Quality Tradeoffs
Balancing the need for high-quality repairs with budget constraints is a perennial challenge. Cutting corners might save costs in the short term, but it risks eroding customer trust and increasing long-term expenses.
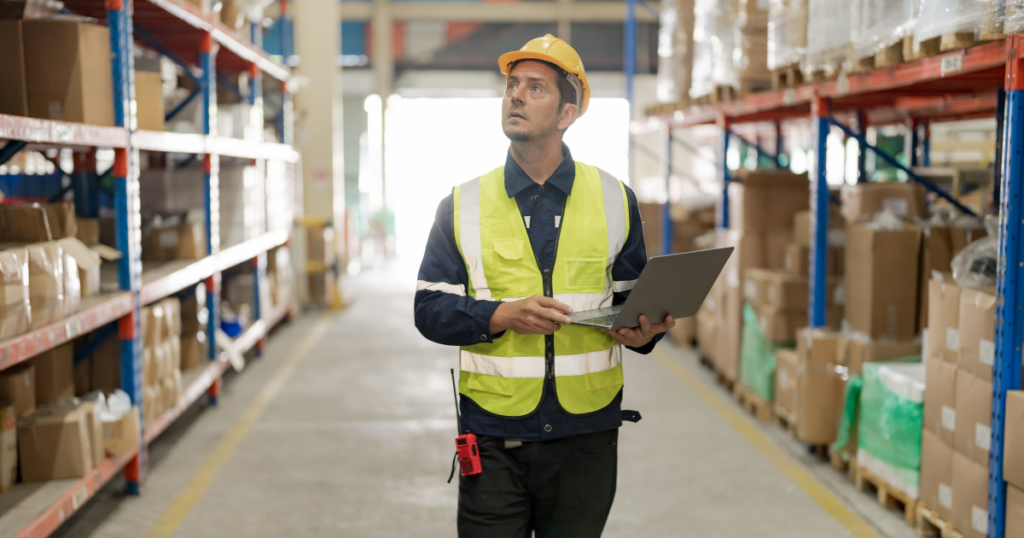
Key Strategies to Achieve First-Time Fix
Achieving FTF excellence requires a strategic approach. Here are the key strategies that can help businesses overcome challenges and elevate their service operations:
- Predictive Inventory Management
Leverage AI-driven tools to anticipate service demands. This ensures that technicians always have the right resources at the right time, minimizing delays and increasing efficiency. This forms a critical component of advanced planning solutions for seamless service parts managementāensuring that technicians always have the right resources at the right time to minimize delays and increase efficiency. - Empower Technicians Through Expertise
Invest in skill development and augmented tools to build technician confidence. Leveraging service lifecycle management software and real-time augmented reality support, businesses can empower technicians to resolve complex issues faster and more effectively. Whether itās through advanced training programs or real-time augmented reality support, empowering technicians leads to faster and more effective issue resolution. - Adopt Proactive Service Models
Shifting from reactive to predictive approaches transforms service delivery. By harnessing IoT, AI in supply chain management, and analytics, businesses can proactively address potential issues before they escalate, driving reliability and customer satisfaction. - Maximize Practitioner Expertise
Baxter Planningās Value Accelerator Program helps businesses achieve their key outcomes faster by partnering with seasoned global experts and planning practitioners. This innovative approach integrates logistic planning solutions and best practices to ensure organizations are future-ready and positioned for first-time fix excellence. Armed with decades of expertise and best practices, the program empowers teams with the knowledge and tools they need for success. By combining Baxter Planningās in-depth industry benchmarking with ongoing R&D innovation, the program ensures your organization is future-ready and positioned for first-time fix excellence.
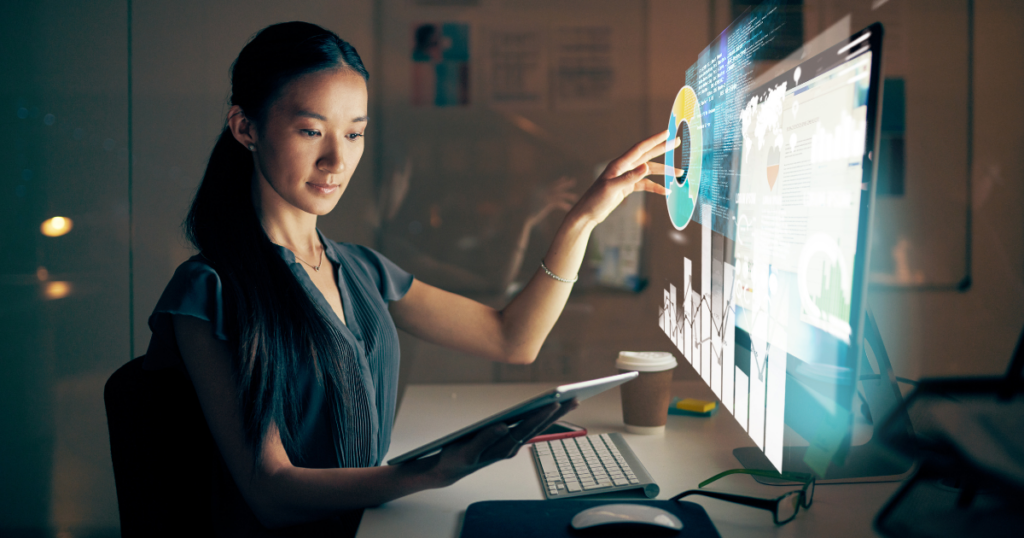
Revolutionizing Service Operations with Cutting-Edge Technology
Emerging technologies are reshaping Service Parts Management, acting as catalysts for achieving unprecedented first-time fix excellence and advancing AI in supply chain management. These innovations are empowering companies to make smarter decisions, act faster, and deliver better results.
Augmented Reality: Bridging the Gap
Imagine equipping your technicians with a tool that doesnāt just show them the problem but lets them experience it virtually before they arrive onsite. Thatās the power of augmented reality (AR). AR allows technicians to visualize issues remotely, collaborate in real-time with technical experts back at headquarters, and pinpoint the exact part needed for a repair. This capability doesnāt just improve efficiencyāit transforms the quality of service you provide.
Machine Learning: Turning Data into Confidence
What if you could predict the parts and solutions needed for a repair with near certainty? Machine learning (ML) makes this possible by analyzing years of service data to identify patterns and predict outcomes. With ML, technicians can confidently order the right components, eliminating guesswork and reducing costly delays. Itās like having a data-driven crystal ball for your service operations.
Business Intelligence Dashboards: From Data to Action
Having access to the right data at the right time is critical in todayās fast-paced world. Business intelligence (BI) dashboards provide a clear, comprehensive view of your service operations, integrating insights directly into scheduling and strategic planning. This data-driven approach ensures that the right parts are in the right place, at the right time empowering your team to meet service demands with precision and speed.
The Metrics That Matter
Organizations achieving FTF success focus on a set of actionable key performance indicators (KPIs) to measure and improve their service delivery:
FTF Rate
A core measure of operational efficiency and customer satisfaction, the first-time fix rate tracks the percentage of service calls resolved on the initial visit.
Parts Availability
Monitoring inventory alignment with service demand helps ensure technicians have the necessary parts to complete repairs the first time.
Customer Satisfaction Scores (CSAT)
Gauging client feedback on the service experience is crucial for identifying areas for improvement and enhancing customer loyalty.
Mean Time to Repair (MTTR)
Tracking the average time it takes to resolve service issues can help organizations maintain a high level of first-time fix performance.
First-Time Fix Excellence: The Strategic Financial Driver
First-time fix rates are critical for driving long-term financial value and customer satisfaction in the Service Supply Chain. Every repeat visit adds unnecessary costs and strains customer relationships, while successful first-time fixes boost trust and operational efficiency. At Baxter Planning, we simplify the path to FTF excellence with purpose-built solutions, advanced AI, and tools tailored for spare parts management. Our expertise helps you optimize inventory spend, make data-driven decisions, and improve service delivery significantly.
Ready to unlock the full potential of your Service Supply Chain? Visit our resource page to learn how we can help you transform first-time fix into a competitive advantage.