The High Cost of Reactive Service Supply Chains
When a critical piece of equipment fails, operations grind to a halt, customers grow frustrated, and costs quickly add up. Scrambling to source replacement parts often leads to delays, reputational damage, and lost revenue—a harsh reality for businesses still relying on outdated, reactive supply chain operations.
Traditional Service Supply Chains operate on a “fix it when it breaks” mindset, leading to:
- Extended downtime due to delayed part availability
- Excess inventory costs from inaccurate demand forecasts
- Customer dissatisfaction from inconsistent service levels
For service leaders, the stakes are clear: inefficient legacy systems and manual processes hinder agility, increase costs, and jeopardize customer loyalty. The question isn’t whether to modernize—it’s how.
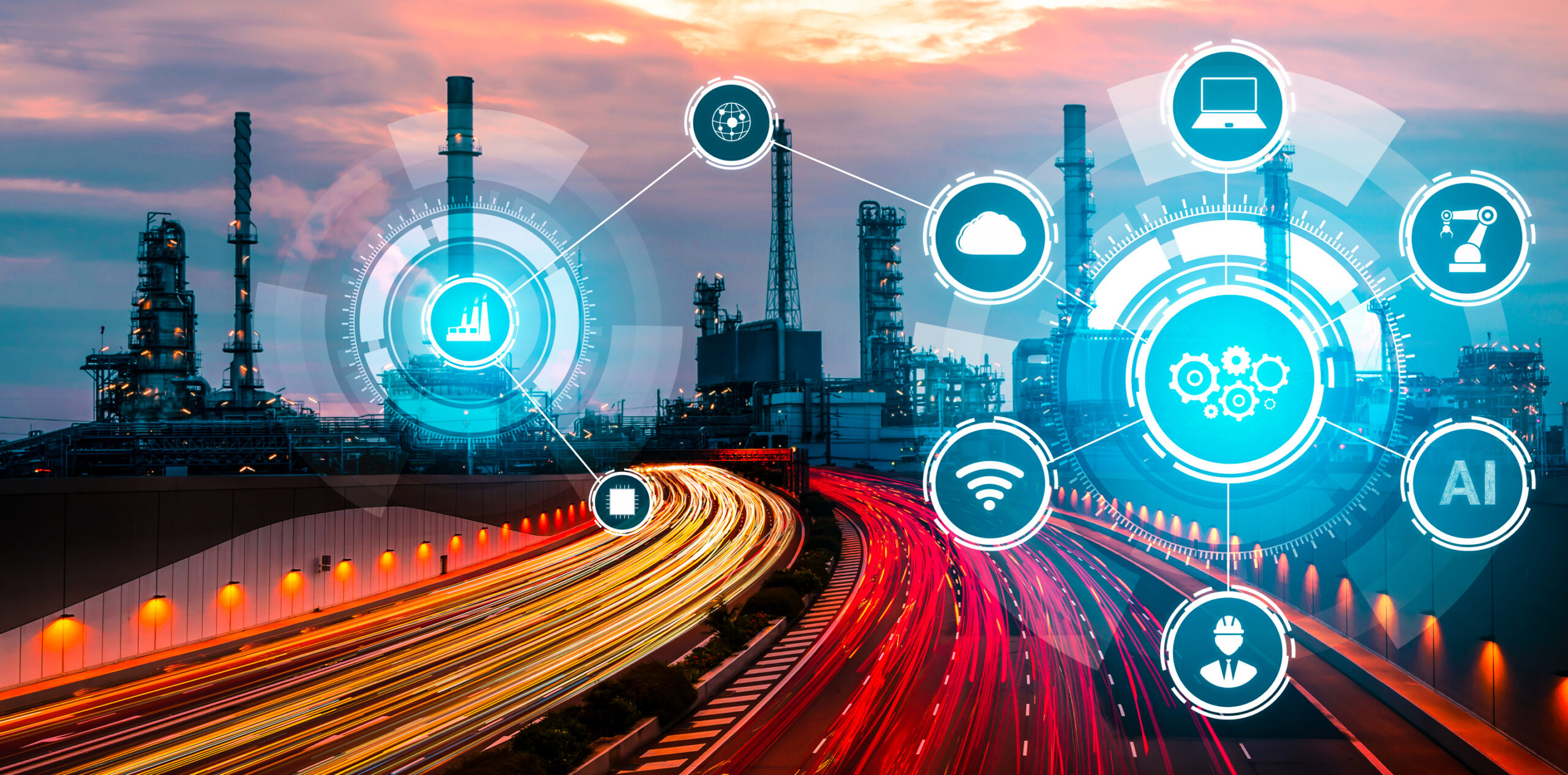
The Shift to Predictive Service Supply Chains
To stay competitive in today’s fast-paced environment, businesses must move beyond outdated, reactive approaches and adopt purpose-built technology that leverage AI. Here’s how to modernize your Service Supply Chain (SSC) for agility, efficiency, and customer satisfaction:
- Smarter Demand Forecasting for Service Parts: Modern Spare Parts Planning goes beyond historical consumption trends, using installed base data, root-cause analysis from order execution, and customer escalation trends to refine inventory planning. Predictive analytics provides actionable insights for demand forecasting, service parts optimization, and inventory management, ensuring the right parts are available when and where they are needed—and at the right cost.
- Predictive Maintenance to Minimize Downtime: Predictive maintenance shifts organizations from reactive repairs to proactive issue prevention. By detecting failure patterns early, businesses can schedule maintenance in advance to reduce costly urgent repairs. The result? Less downtime, improved service reliability, and lower maintenance costs.
- Service Execution at the Speed of Business: Optimizing service parts and Field Service Management is critical to meeting SLAs. AI enables businesses to predict demand surges, optimize technician trunk stock, and improve first-time fix rates, ensuring efficient service execution, faster problem resolution at a lower cost, and smaller carbon footprint.
BaxterPredict: Driving ROI with Predictive Intelligence
The BaxterPredict platform empowers businesses to transition from reactive problem-solving to predictive, data-driven execution. It’s the only end-to-end solution that provides visibility into the entire Service Supply Chain—from Spart Parts Planning to order execution to resolving part availability issues. Here’s how it delivers measurable ROI:
Eliminate Stockouts, Reduce Inventory Costs
BaxterPredict’s Total Cost Optimization approach, prevents stockouts while reducing excess inventory. Using proprietary modeling, it determines optimal target stock levels by factoring in qualitative and quantitative cost elements—balancing inventory costs with the risks and expenses of stockouts. This approach helps businesses lower carrying costs by 35% while ensuring critical parts are available when needed.
Proactive Issue Resolution for More Efficient Services
Predictive alerts identify potential service disruptions days in advance, allowing teams to resolve issues before they impact SLAs. With these new insights, companies are realizing up to 12% reduction in annual inventory spend, while improving service efficiency and safeguarding customer trust.
Data-Driven Insights to Drive Customer Satisfaction
BaxterPredict leverages continuous feedback loops within the platform to automatically incorporate order execution and part availability data into the spare parts plan to build resiliency and reduce future escalations. With this unique approach to planning, organizations see an 8 to 10% improvement in customer satisfaction (CSAT), minimizing service delays and ensuring faster response times.
Seamless AI Models for Scalable Growth
BaxterPredict takes the guesswork out of long-range planning by leveraging purpose-built models for New Product Information (NPI) and Last Time Buy (LTB) forecasting helping companies achieve 95% accuracy while reducing overbuys and underbuys. Pre-built integrations with ERP, CRM, SCM, and 3PL solutions accelerate deployment and maximize value—ensuring businesses can scale their service operations without added complexity.
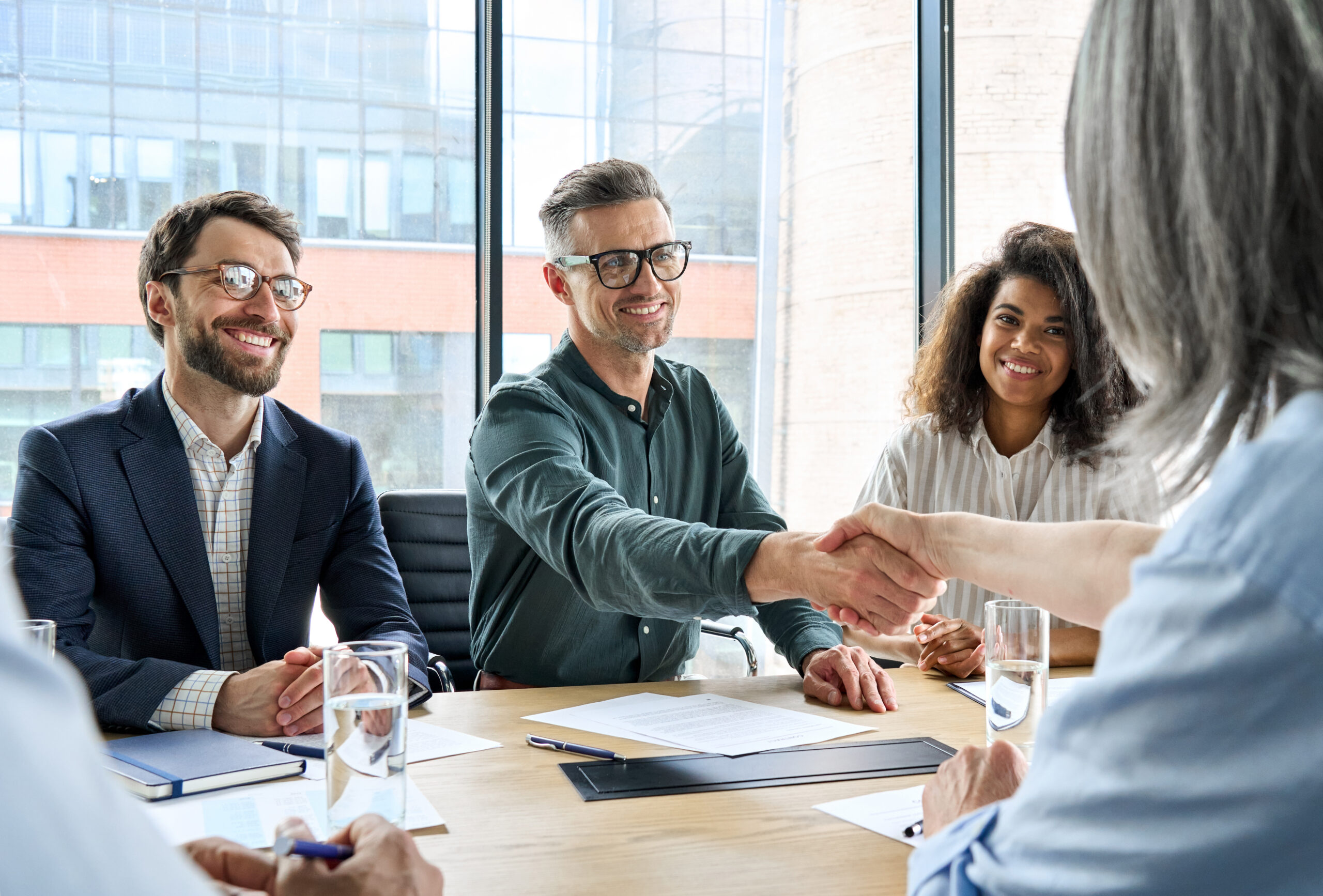
Beyond Technology: The Right Partner for Predictive Service Supply Chains
Adopting predictive intelligence isn’t just about the technology—it requires deep expertise and industry knowledge to apply it effectively.
This is where Baxter Planning thrives. We don’t just implement AI—we help businesses navigate their journey, ensuring solutions are tailored, actionable, and deliver measurable results.
- Proactive Risk Mitigation: AI identifies supply chain vulnerabilities—from supplier delays to demand fluctuations—before they impact operations. But predicting disruptions isn’t enough. Baxter Planning applies insights through industry-proven methodologies, ensuring businesses have the right contingency plans in place to reroute inventory, secure alternative suppliers, and maintain service levels.
- Dynamic Resource Allocation: Real-time insights continuously refine inventory distribution and Service Parts Planning, but AI alone isn’t enough. Our SSC experts help businesses balance cost, speed, and reliability without overextending resources. By adapting service strategies to market shifts, organizations can optimize resources, meet growing demands, and drive efficiency.
- End-to-End Visibility: Integrating and transforming data from IoT, ERP, and other systems into a single platform provides a complete view of customer orders, inventory levels, issue resolutions, costs, and more. Our AI models are applied effectively, helping businesses optimize workflows, track key metrics, and improve supplier accountability—turning raw data into high-impact insights to drive better decision making.
- Continuous Optimization: Robust data feedback loops continuously improve demand forecasts, refining services based on operational insights. For example, if a service part fails more often in humid climates, the system adjusts regional inventory levels and triggers predictive maintenance alerts—proactively preventing failures. We help clients integrate advanced technology into daily operations, transforming data into adaptive, long-term value.
- Seamless Scalability: Scalable platforms adapt to company growth and shifting market conditions—from inventory shortages to service contract expansions. But true scalability requires more than technology—it demands a strategic partner who understands your business, risks, and long-term goals. With Baxter Planning’s deep expertise, businesses can seamlessly integrate AI-driven decision-making, ensuring their SSC evolves without compromising service quality.
Future-Proofing Service Supply Chains: The Road to AI-Driven Excellence
AI is no longer an emerging trend—it is the foundation of next-generation Service Supply Chains. Organizations that embrace predictive intelligence, automation, and real-time optimization will lead the industry, while those clinging to outdated methods will struggle to keep pace.
BaxterPredict equips businesses with AI-powered solutions that optimize inventory, reduce disruptions, and drive lasting competitive advantage. Don’t wait to modernize your operations—stay ahead of the curve.
Explore our resource hub to learn how purpose-built technology can future-proof your Service Supply Chain and position your organization as an industry leader.