If you’re using an ERP system to manage Service Parts Planning, chances are you’re working harder than necessary. From constant report pulling to patching together spreadsheets, your team is doing the best they can with a system that wasn’t built for this type of planning. While ERP platforms are essential to core business functions, they were never designed to handle the unpredictability and unique demands of aftermarket service.
Today’s Service Supply Chains are dynamic, distributed, and data-driven. Meeting service level agreements (SLAs), keeping customers satisfied, and controlling costs all depend on smarter planning. But ERP systems, which were developed for linear manufacturing processes, can’t keep up with the complexity of service operations.
Why ERP Can’t Optimize Spare Parts Inventories
ERP systems fall short in several areas that are essential for effective Service Parts Planning.
- Manual and Disconnected Workflows
Planners often spend hours gathering reports, reconciling spreadsheets, and reacting to yesterday’s issues. This slows down response times and leaves little room for strategic work. ERP systems lack the real-time visibility and unified workflows that modern planning requires. - Inflexible Planning Logic
Most ERP tools rely on fixed reorder points and basic forecasting models. In service environments, however, demand is unpredictable. Failure rates fluctuate, usage varies, and product lifecycles impact when and where parts are needed. ERP systems are not designed to adapt to these changes, making it difficult to keep the right parts in the right locations. - Missing Service-Specific Capabilities
Service Parts Planning involves far more complexity than traditional manufacturing planning. ERP systems lack critical features such as:
- Dynamic part chaining and substitution logic
- Reverse logistics and repair loop planning
- Forecasting from multiple demand sources (failures, maintenance, transfers, sales)
- Inventory positioning based on SLAs and installed base data
- Root cause analytics to explain service misses
- Lifecycle and end-of-life (EOL) planning for long-term product support
These limitations increase inventory costs, reduce service performance, and force planners into reactive mode.
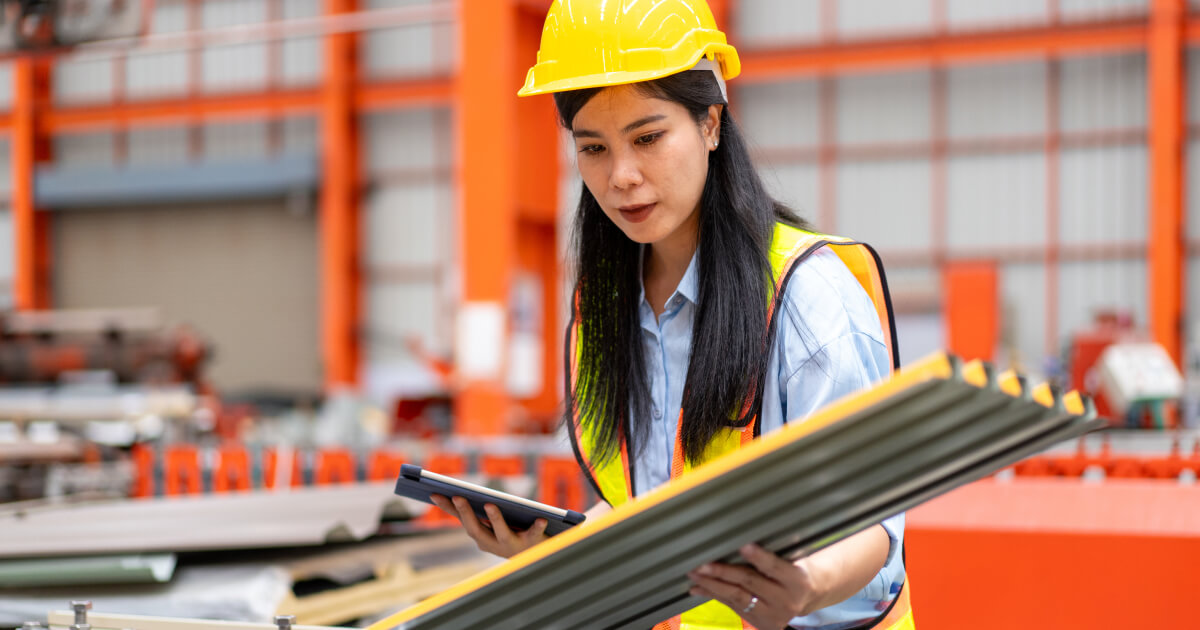
From Reactive to Predictive: Rethinking the Role of Service Planning
Traditional ERP systems often keep Service Parts Planning (SPP) stuck in reactive mode. You only find out there’s a problem, like a stockout or a missed SLA, after it’s already impacted your customer. By then, it’s too late. Costs go up, escalations pile on, and planners are left reacting instead of improving.
Modern inventory planning software changes this. With a predictive approach, planners can stay ahead of demand, position parts where they’re needed most, and reduce last-minute surprises. It’s a smarter way to plan—and it’s what today’s Service Supply Chain solutions require.
More than just improving operations, predictive demand planning elevates the role of service across the business:
- Service becomes a profit lever. By lowering expedite costs and improving first-time fix rates, and combining that with the higher margins of service contracts, service becomes a strong revenue driver.
- Data becomes actionable. With better demand forecasting and scenario modeling, planners can focus on high-impact decisions instead of chasing down reports.
- Service becomes essential to customer experience. Predictive demand planning software ensures the right part is in the right place; supporting SLAs, improving first-time fix rates, and strengthening customer trust.
To achieve this shift, organizations need more than what an ERP can offer, even with expensive customizations. They need planning tools built specifically for the complexity of service—tools that support dynamic environments, adapt to change, and provide the visibility required for true Service Parts Planning optimization
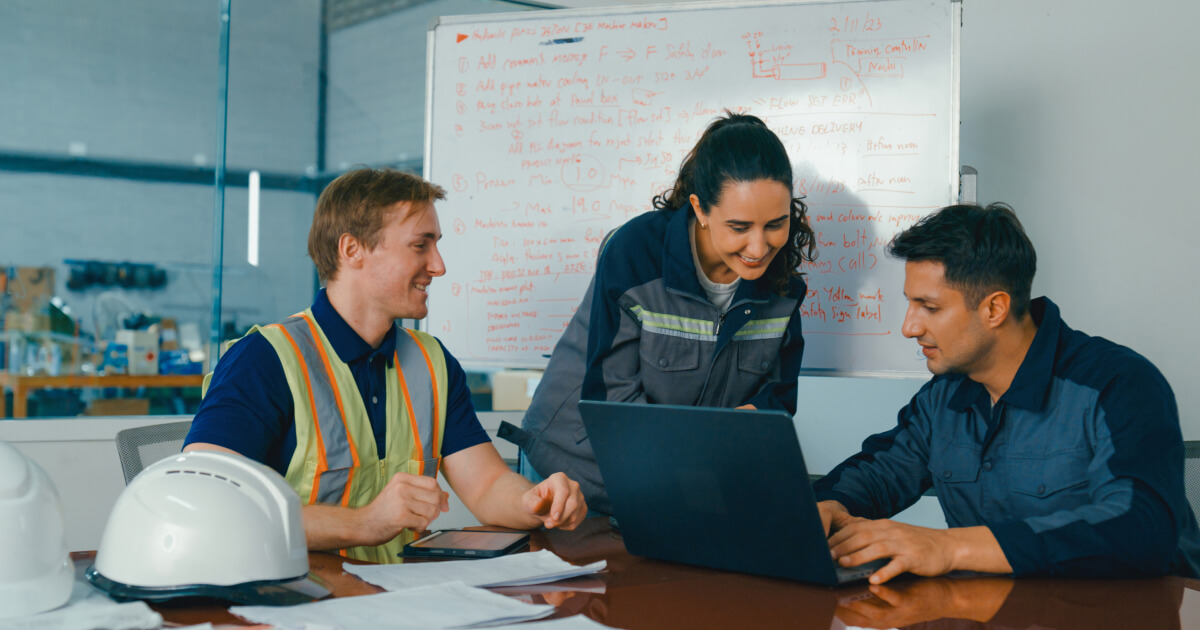
How BaxterPredict Enables Smarter Planning
Baxter Planning has been dedicated to the Service Supply Chain for more than 30 years. That’s why BaxterPredict, our end-to-end predictive planning and execution platform is designed specifically to address the complexities ERP systems can’t handle.
With BaxterPredict, you gain:
- Predictive forecasting using real-time service signals and lifecycle trends
- Automated planning for part chaining, repair loops, and inventory positioning
- SLA-based inventory optimization tailored to business impact and urgency
- Total Cost Optimization to weigh trade-offs between stocking, sourcing, and fulfillment
- Built-in root cause analytics to reduce exceptions and refine planning over time
Want to see the difference?
Download the BaxterPredict vs. ERP solution brief for a side-by-side comparison of planning capabilities.
Where Are You on Your Service Parts Planning Journey?
Making the shift from reactive, ERP-driven planning to a predictive, service-optimized approach doesn’t happen overnight, but it starts with knowing where you stand.
Whether you’re just beginning to question the limits of your ERP system or already pursuing smarter planning, understanding your current capabilities is key to building a better strategy.
Get the Maturity Matrix eBook and take the next step toward turning your Service Supply Chain into a competitive advantage.