In traditional supply chains, planning often begins with historical demand patterns. However, in the Service Supply Chain, where customer downtime can lead to significant penalties and erode loyalty, planning must start with the customer’s equipment. This is where Installed Base Planning becomes essential.
By understanding where assets live, how they are used, and when they might fail, organizations can shift from reactive stocking to proactive service readiness.
Service Supply Chain Forecasting
Installed base visibility enables planners to move beyond generalized statistical models. Instead of treating all demand as uniform, Installed Base Planning allows segmentation based on asset-specific factors such as age, usage intensity, maintenance history, and environmental conditions. It uses a calculated engineering failure rate based on the number of equipment installed and the times that a part has been used to service the installation. This increases the accuracy to understand MTBF (mean time between failures) and MMTF (mean time to failure).
For instance, the same model of a generator operating in a hot, dusty mining site will have different service needs than one in a climate-controlled facility. Or the same model of elevators using the same components, installed in buildings with a different number of floors.
This implies that wires, hoses, cables, etc, materials that have a unit of measure, need to be planned differently. Installed Base Planning allows that capability. This level of detail empowers planners to tailor forecasts for more accurate and efficient inventory deployment.
Supporting this approach, Baxter Planning emphasizes that relying solely on historical data assumes customer needs remain consistent, which is often not the case. They advocate for incorporating installed base data to improve forecast accuracy and service responsiveness.
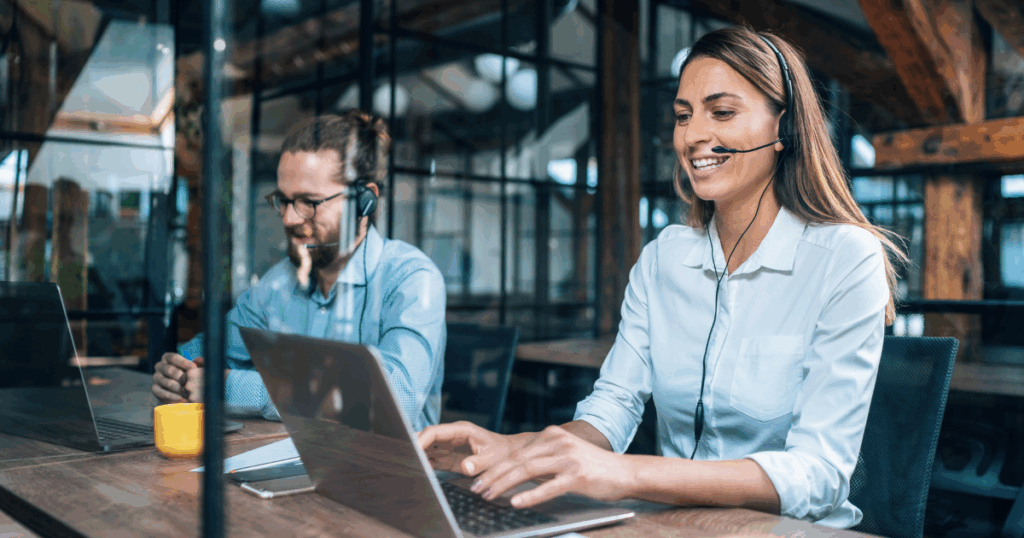
How to Optimize Spare Part Distribution
With insights into the installed base, organizations can make informed decisions about where to position inventory.
Rather than distributing high-value parts across multiple locations “just in case,” planners can place parts where they are statistically more likely to have a demand event occur in that specific area, based on knowing historic failures. This improves part availability, reduces shipping time and cost, and helps ensure that service level agreements (SLAs) are consistently met. It also supports better field service outcomes by increasing the likelihood of a first-time fix.
SupplyChainBrain notes that leveraging installed base data allows for the creation of a supply chain and inventory strategy aligned with predictive analytics, enhancing the ability to anticipate failure and repair requirements.
Enabling Predictive and Preventive Service
Installed Base Planning also serves as a stepping stone to predictive maintenance strategies. When installed base data is connected to condition monitoring or IoT systems, service organizations can anticipate failures, ensuring the parts are ready in advance. An additional benefit is that it enhances maintenance planning accuracy by allowing materials to be used closer to their actual wear limits, rather than being replaced too early.
With Installed Base Planning, you therefore minimize emergency logistics, lower total service cost, and improve technician efficiency. With AI-driven insights layered in, the entire planning function evolves into a model that anticipates needs rather than simply responding to them.
McKinsey highlights that advanced planning systems, when integrated into an optimized end-to-end process, offer proactive strategies for anticipating challenges and customer needs, providing newfound visibility.
A Differentiator for Customer Experience
Ultimately, Installed Base Planning is not just an operational improvement; it is a driver of customer trust and loyalty. Clients recognize that their service provider understands their equipment and is prepared to act quickly and effectively. This perception translates into higher contract renewal rates, upsell opportunities, and a competitive edge in industries where uptime is critical.
Installed Base Planning provides service leaders with the confidence to deliver on promises consistently.
Bain & Company underscores the value of installed base management, noting that it can generate significant value by adding new revenue streams and enhancing customer relationships.
How to Get Started with Installed Base Planning
The team at Baxter Planning is deeply experienced in Installed Base Planning, both through our purpose-built BaxterPredict platform and through the decades of practitioner expertise that our Planners possess and offer via Planning as a Service. Contact us today to learn how you can turn your installed base data into a powerful engine for predictive service, increased uptime, and greater customer loyalty.