Navigating the Service Experience Storm with Smarter Planning
In today’s Service Supply Chain, unpredictability is no longer an exceptionāitās the norm. Organizations managing service parts face constant challenges: balancing service levels with inventory costs, mitigating supply chain disruptions, and ensuring the right part is available at the right time.
As Baxter Planningās Chief Innovation Officer, Chad Hawkinson pointed out in a recent podcast:
āYou can have all the data in the world, but without the right predictive analytics for inventory, you’re still just guessing.ā
The Changing Landscape of the Service Supply Chain
Unlike forward supply chains, Service Parts Management requires a fundamentally different approach. When critical equipment fails, service organizations must restore uptime quicklyāoften within hoursāwhile controlling inventory and shipping costs. The impact of downtime extends far beyond part replacementāit includes productivity loss, revenue disruption, and customer dissatisfaction.
Chad explained that the industry is undergoing a transformation:
āWe focus specifically on spare partsāhelping organizations meet service obligations while balancing service levels and inventory cost.ā
Customer expectations are rising. Same-day service, two-hour response windows, and zero tolerance for stockouts have become the new standard. Organizations can no longer afford to rely on static forecasts or excess inventory. A smarter, data-driven planning approach is required, and thanks to innovation, a better way is available.
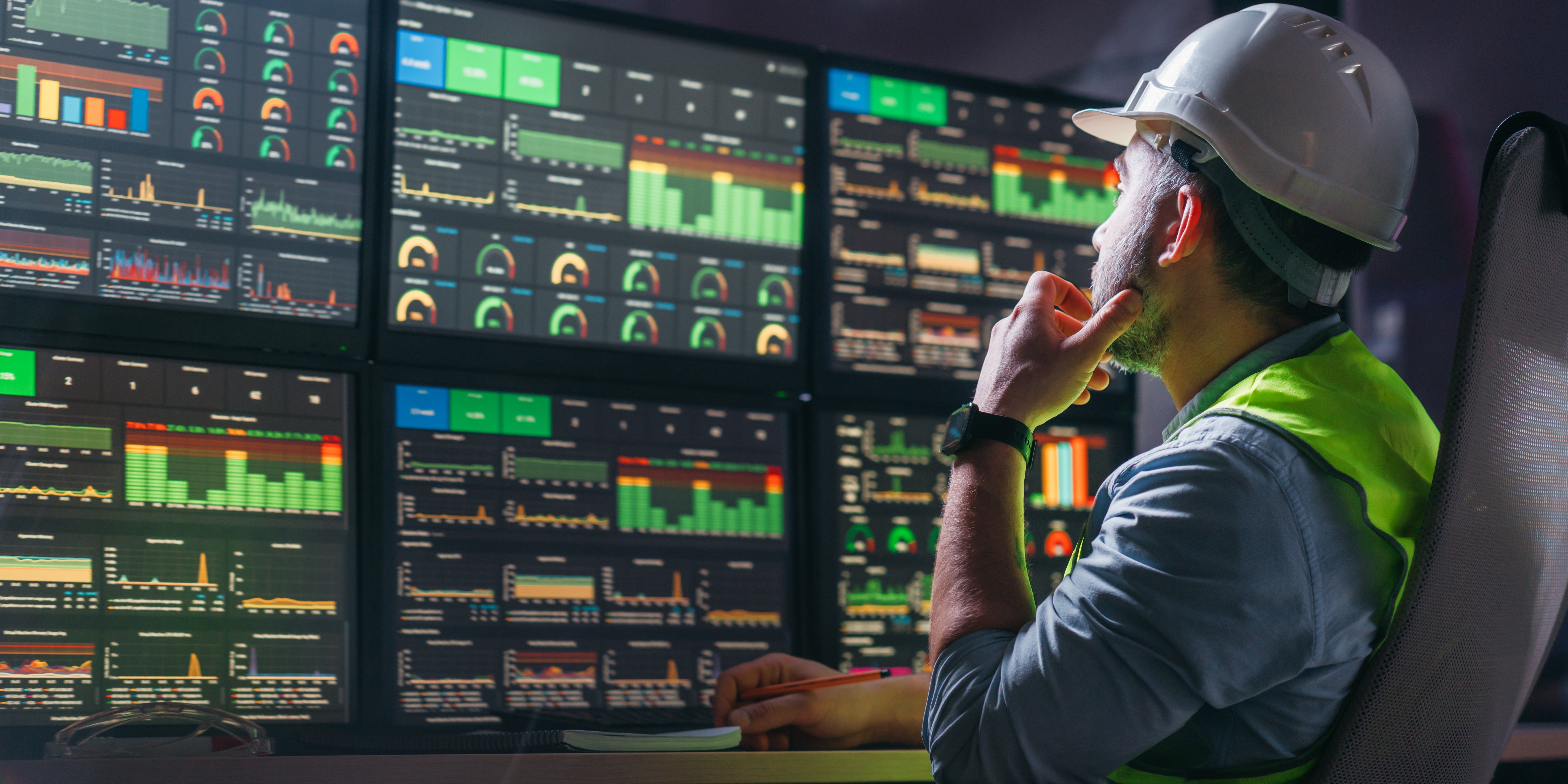
The Power of Predictive Analytics and Artificial Intelligence
Static spreadsheets and legacy systems canāt keep pace with the dynamic needs of todayās service environments. Thatās where Service Supply Chain software like the BaxterPredict platform delivers measurable value.
By applying predictive analytics for spare parts management, the platform enables organizations to optimize inventory, mitigate risks, and adjust dynamically to real-time disruptions. It integrates advanced models across multiple data streams to improve planning accuracy at scale.
Chad emphasized, “What sets apart industry leaders is not just having data but knowing how to use it intelligently. Demand planning software needs to evolve beyond static models to dynamically adjust based on real-time inputs.”
BaxterProphet, part of the BaxterPredict platform, delivers smarter inventory planning by forecasting demand, adjusting dynamically to challenges, and aligning inventory levels with business goals.
Key benefits include:
- Smarter, more accurate spare parts demand forecasting
- Real-time visibility into disruptions
- Decision support for balancing inventory costs with service level agreements
- AI-powered long-term planning for new, complex, and aging assets
In practice, organizations have been able to reduce inventory by an average of 25% while improving service levelsāa critical balance that directly impacts the bottom line.
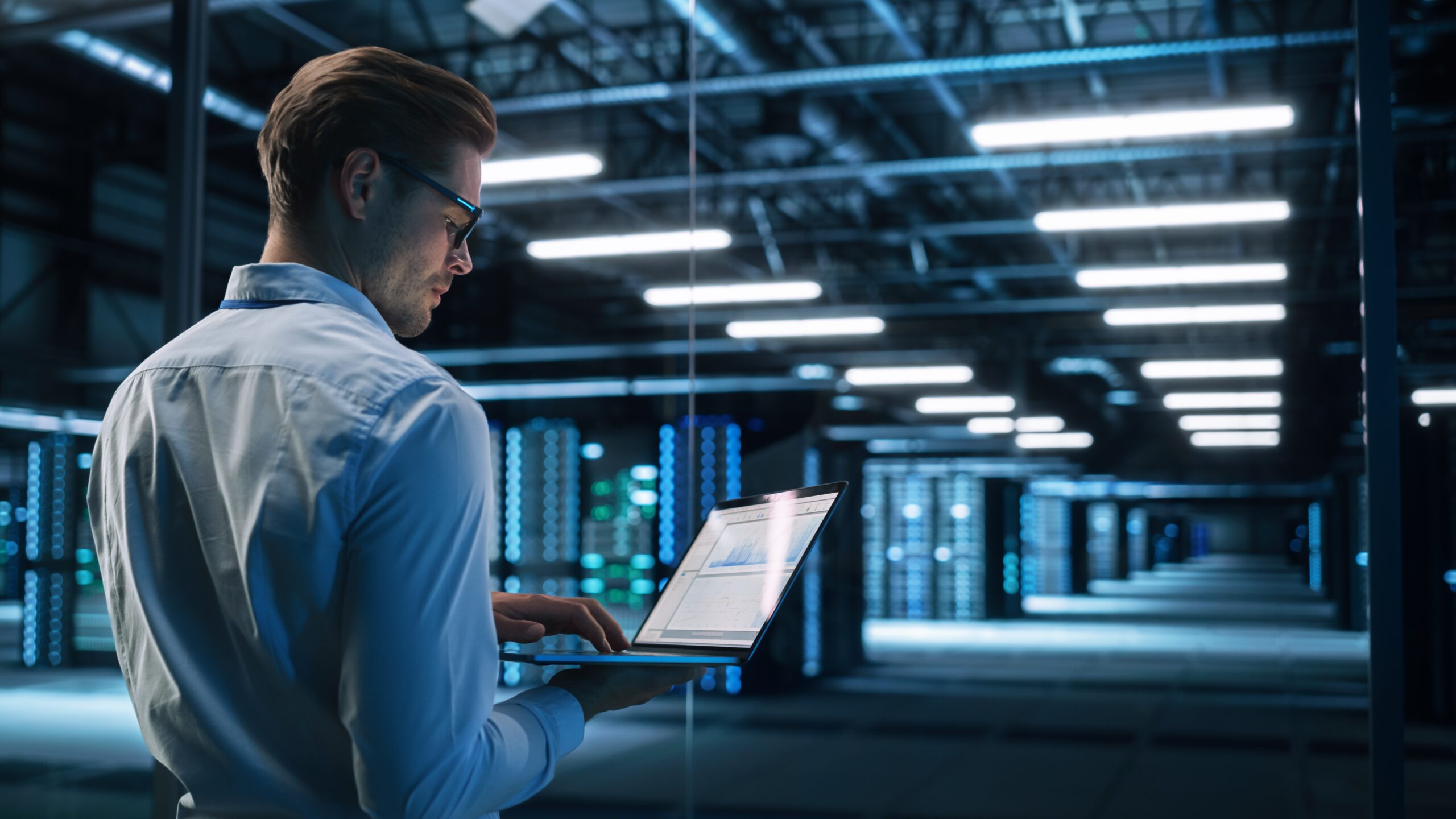
From Reactive to Proactive: Inventory Replenishment Optimization
For many organizations, replenishment is still reactiveātriggered only after a shortage or service failure. Baxter Planning enables a strategic shift toward inventory replenishment optimization, giving planners the tools to stay ahead of demand and respond with agility.
With supply chain forecasting software built for the service environment, organizations can:
- Improve First-Time Fix Rates: Ensuring that technicians arrive with the correct parts, reducing the need for repeat visits.
- Cut Stockout Costs: With a reduction of nearly $300 million in stockout expenses reported by customers, every minute counts when managing critical parts.
- Optimize Inventory Levels: Achieve leaner inventories with improved turnover rates, supported by continuous data monitoring and analytics.
In 2024 alone, Baxter Planning customers collectively saved over $600 million in inventory costs and reduced stockout-related losses by nearly $300 million.
As Chad noted, “Service Parts Planning isnāt just about reducing excess inventory. It’s about ensuring uptime and reliability without unnecessary costs.”
Achieving the Service Experience Advantage
By combining intelligent software with deep supply chain expertise, Baxter Planning delivers a Service Experience Advantage. Beyond just delivering software, our approach includes:
- Implementation Best Practices: A collaborative model where experts guide customers from the sales process through implementation and beyond, ensuring that best practices are adopted.
- Dedicated Expertise: Regular, ongoing reviews of operating metrics, enabling proactive adjustments and continuous optimization.
- Partnership Programs: Partner with our planning experts, benchmark performance against peers and participate in advisory boards to drive the future of our solutions.
- Rapid ROI: With many customers seeing significant benefitsāincluding a 16% reduction in inventory within six monthsāthis approach demonstrates a strong return on investment early in the deployment cycle.
As Chad succinctly put it, “Inventory optimization isnāt about having less stockāitās about having the right stock, where and when you need it.”
Looking Ahead: Future-Proofing Service Parts Planning
As market conditions evolve, one thing remains clear: managing service parts through outdated methods, like spreadsheets or a customized ERP, is no longer sustainable. Organizations must adopt specialized solutions designed for the complexity of aftermarket operations.
Purpose-built Service Supply Chain software provides the agility, insight, and efficiency that todayās environment demands. Combined with intelligent automation and expertise, this approach empowers service teams to proactively manage disruptions and deliver a differentiated service experience, even in the most complex of environments.
Is your organization ready to move beyond guesswork?
Explore how BaxterPredict can modernize your approach to inventory optimization, improve resilience, and optimize service performance at scale.