The last few years have shown us how irritating and downright devastating a shortage of products can be. And we’ve learned that experiencing shortages can cause some wild strategies for ensuring you don’t stockout in the future, i.e., the hoarders of March 2020 piling toilet paper up to the ceiling in their garages! However, there is a fine line between being well stocked to supply future needs and being overstocked with excess resources that are wasting space and money. While the toilet paper hoarders have a simple strategy for using up their excess inventory, knowing the best way to utilize excess spare parts is often not as straightforward.
That’s why in our latest version of BaxterProphet, our Service Parts Planning software, we released a new Excess Utilization feature that helps customers utilize their excess spare parts inventory in a smart and effective way.
From Stockout Cost to Strategic Opportunity
At some point, we know our customers will deal with excess inventory; it’s an inevitable aspect of the Field Service industry. Excess inventory is a big deal though. Not only is excess inventory a result of investing more than needed up front, it becomes an expensive, ongoing burden to manage. Companies are forced to answer the difficult questions of: Do we continue to store this excess inventory and hope we use it? Should we try to sell this excess inventory? Can we recycle the excess inventory? Should we scrap the excess inventory and take a loss?
Disposing of spare parts requires resources for proper disposal and can sometimes result in inventory ending up in landfills, which is not sustainable for the environment. However, if you don’t dispose or recycle the excess and aren’t able to sell it, the other option is that you pay to keep your equipment in storage. This isn’t cheap, and we know that stored parts eventually become obsolete or expire anyway.
Our Excess Utilization feature focuses on addressing the main pain points around excess inventory: storage and useability. With the Excess Utilization feature, customers can configure BaxterProphet to help distribute excess inventory where it’s most likely to be used in their logistics network. Afterall, that initial investment was made for a reason—because customers might need the parts. And if you’re already paying to store that excess inventory, you might as well keep it in an ideal place.
Additionally, most FSLs already have a minimum requirement of inventory as a safety net. Intelligently distributing excess inventory to the FSLs using Excess Utilization helps you strategically meet this requirement.
Cut Costs, Elevate Customer Service
In today’s world of rising interest rates, inflation, and high gas prices, you need to be as cost savvy as possible. Our Excess Utilization feature helps you cut transportation costs by placing your inventory closest to the destination where it is most likely to be used. And while all companies could stand to operate more cost efficiently by regenerating the value of their existing investments, businesses with policies that include target stock levels in the profit and loss (P&L) can especially benefit from this.
Applying Excess Utilization logic will lessen the negative impact of having extra reserves as target stock levels drop. But perhaps the best perk of Excess Utilization is that it allows you to use your inventory for its original purpose: to provide excellent service to customers. You’ll be stocked and ready for their needs without having to scramble or splurge on expedited shipping.
Learn More & Get Started
In Field Service, we know it can feel like you must strive for perfection and precision at every turn or risk a chain of unfortunate events being unleashed. But we all need a margin of error to operate in, and that’s what Excess Utilization will help create. It’s a buffer for the times when life unfolds as it does, which is messy and unpredictable.
To learn more about Excess Utilization, click on “What’s new in Prophet” in BaxterProphet’s eLearning center. If you’d like to take advantage of this new enhancement, please submit a request to our Service Desk.
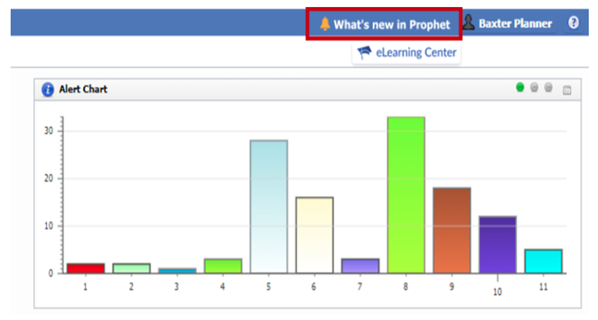