Spare Talk Episode 4 Recap
Episode four of Spare Talk hits a subject that’s on many people’s minds: supply chain disruptions. We’re experiencing them globally, and they’re a HOT topic. But how do they impact the Service Supply Chain?
Mike and John are seeing this come up with almost every one of our customers, but it manifests in surprisingly different ways.
For instance, Mike was talking to the individual who manages the planning for a central distribution center. He has some purchase orders with a leadtime of five to six weeks. They got on a container ship, and will arrive with no issues. But other parts coming on different ships are still stuck somewhere. He has no idea when they’ll show up, and in general, he can’t predict which of his orders will end up having issues.
How to Plan for Indeterminate Leadtimes
In response to that scenario, John commented that even once the supplier puts their order on the ship, they don’t know anything. So, the question becomes: How do you plan for indeterminate leadtimes?
Mike and John have some suggestions:
- Know where your parts are coming from, and which ones have the highest potential to see issues.
- Plan with the expectation that you’ll experience some disruption.
- Consider faster freight options for certain limited assets.
- Remember that your original order will still show up, even if you put in a new, expedited order.
- Look into alternate sourcing, even newer options, like 3D printing.
- Rebalance by tapping into your own network – you could have excess parts sitting in locations where they’re not needed.
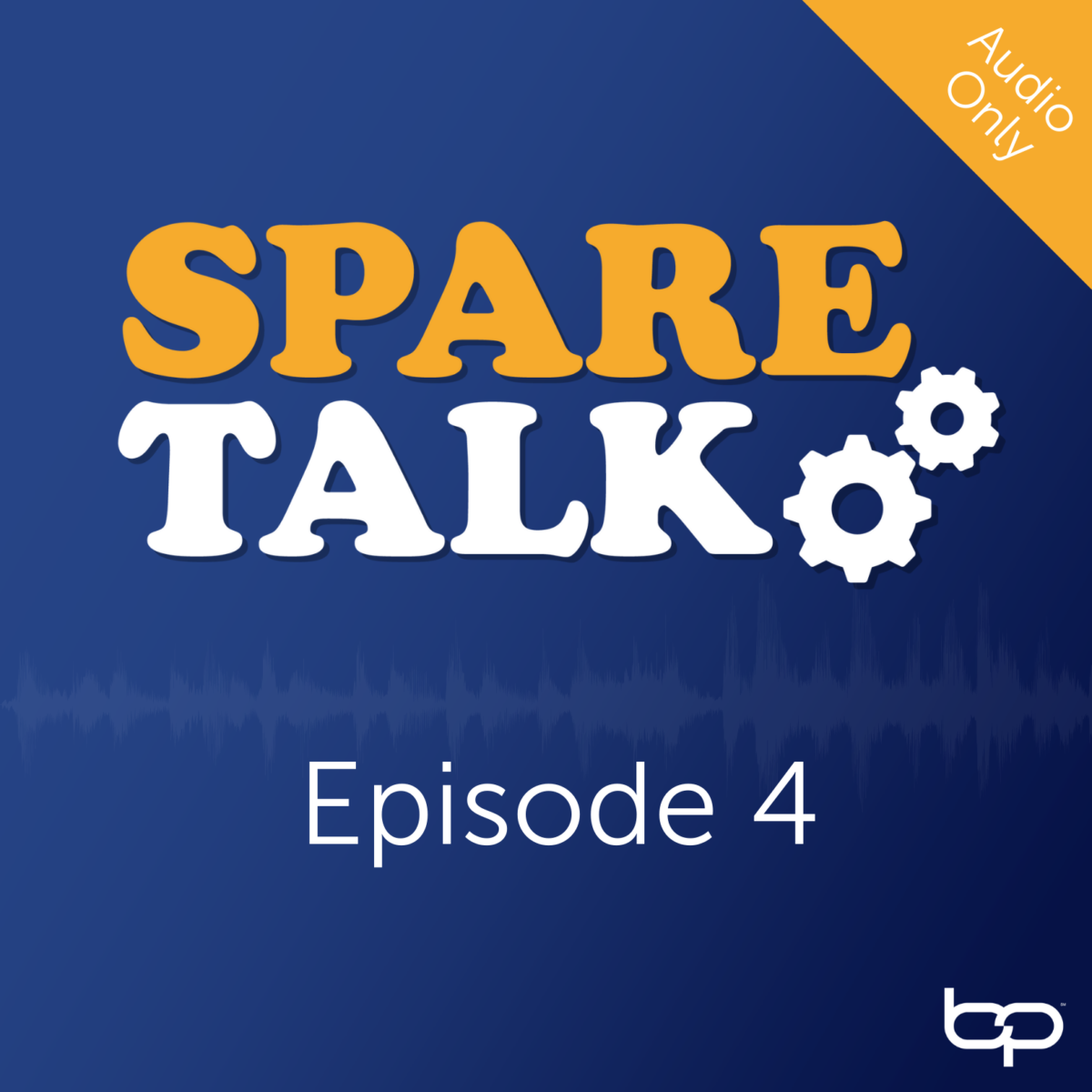
There are a lot of issues going on right now, and one fix might work for one company, but not for another. In some cases, even making extra orders to safeguard your future stock levels can worsen the bottleneck because you’ve piled onto the manufacturer’s queue or added the need for another shipping container. It’s complex. However, we can all hope that these supply chain disruptions are just the Grinch this holiday season, and that Cindy Lou Who is right around the corner to make its heart three sizes (or ships!) bigger.
Reverse Logistics
Reverse logistics is a major differentiator between Service Parts Planning and other supply chain environments. There are a lot of decisions that go into defective inventory. Do you need to repair it? If so, do you need an internal repair or an external repair? Either way, a service parts planner needs to know what defective material will return. Not every piece of defective material gets returned, and of the material that is returned, not all of it’s repairable.
John suggests starting with the yield process; less than 100 percent of what you send out comes back, and less than 100 percent of what comes back will be usable. Then Mike makes the point that you may need to go through this education process if you or your boss is new to reverse logistics in the service parts world. It involves extracting broken parts from equipment so you can monetize and reuse it, which is a unique undertaking.
There are different types of reverse logistics streams. The most traditional is when a service technician goes on site, fixes a piece of equipment, and removes something from the equipment that’s fixable (and likely expensive). It often includes things that cost thousands of dollars but can be repaired for only fifty; saving the company a lot of money.
The second type involves “good” returns from a customer when you’re in a dealer distributor situation. In both cases, you should have a screening process, as the technician may send back three parts that still operate, and one part that needs repairs, for instance.
Reverse Logistics Process
From a planning perspective, how do you handle inventory that comes back and really refine your reverse logistics cycle? You should net it into the forecasting of your planning process. And for that, you need a system that can forecast when a certain percentage of each specific part will need repairs before it can go back out, affecting its leadtime. With this knowledge, you can identify when to bring new inventory into your system and prioritize those repairs over new purchases, as it’s less expensive to do so. However, if you send the repairs out of house, you must put other considerations into your system.
By refining your organization’s unique reverse logistics process, you save time and money. Plus, you can help make your supply chain more sustainable, as there’s a green aspect to reverse logistics.
Spare Talk Runs on Questions & Feedback
Spare Talk is brought to you by listener comments and questions, so please send YOUR feedback to sparetalk@baxterplanning.com. Thank you for supporting Spare Talk!
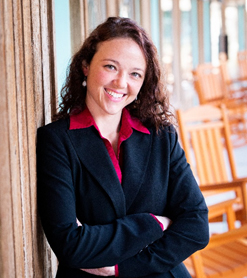
Lindsey Rose
Marketing Director
Lindsey is a relatively new addition to the Baxter Planning team, running the company’s marketing activities like webinars, email communication, and you guessed it – the Baxter Planning Blog.
With more than eight years in B2B Marketing, Lindsey enjoys finding unique ways for a company to not only stand out, but to bring true benefit a company’s customers and the industry as a whole. She finds the Baxter Planning team especially amazing to work with because of the deep passion and knowledge held by the subject matter experts and everyone at the company.
Lindsey stays plenty busy outside of work, spending time with her husband and their two toddlers. They spend lots of time at playgrounds and going for walks with their dog.