Total Cost Optimization – Part 2: Inventory and Instability Costs
The costs of too much inventory and the costs of an unstable plan
In part 1 of this series devoted to Total Cost Optimization, we discussed the operational costs of not having a part in the right place, and how these costs need to be considered in the Service Parts Planning Optimization process.
As we continue our exploration of cost optimization, we consider two additional costs that must be balanced in the optimization process: inventory costs and instability costs.
Inventory Costs
Everyone knows that inventory costs money. Look at the financials of any publicly traded company, and you’ll see inventory right there in their financial statement.
Parts planning is usually viewed as strictly a balancing act of inventory versus service level. This is often depictedin terms of an exchange curve graph, which shows that as service level approaches 100%, the inventory investment to achieve incremental service level improvement grows exponentially.
While it’s important to understand the key planning concept that service gains become smaller and smaller as you approach 100%, it’s also important to understand how those inventory investments impact your company and, in the case of Total Cost Optimization, how much other operational expenses are reduced as inventory is added.
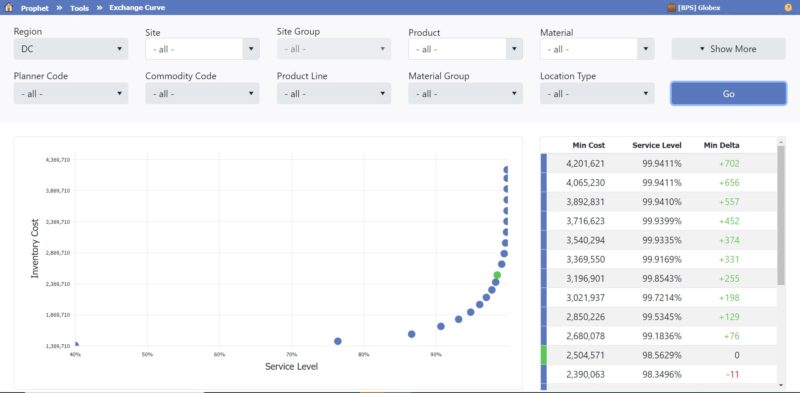
There are multiple categories of inventory costs that should be considered in a Total Cost Optimization approach for service parts. This is not a full list, but it represents some key categories of the cost of on-the-shelf inventory:
- Carrying cost: This is sometimes described as “opportunity cost” or “the cost of money.” If your company has invested in inventory, then that investment is sitting on a shelf, depreciating rather than growing. If too much is invested in inventory, then that money is unavailable for other parts of your business, such as investing in research and development (R&D), or buying back company stock. Excessive inventory investment is a lost opportunity for that cash to do more valuable things.
- Risk of obsolescence or excess: Any investment in inventory needs to consider the risk that the inventory will eventually become obsolete. This is a worst-case scenario, not only does your organization risk needing to scrap a valued asset, but there are finance and write-off cost implications. There is also the cost of the scrap exercise itself, as environmentally sound disposal may be expensive depending on the type of asset.
- Warehousing costs: More inventory means more warehouse space. In an environment where a third-party logistics (3PL) company is providing warehousing, paying for inventory space by the square foot is common. Inventory that’s on the shelf needs to be periodically counted, and that takes warehousing personnel time investment as well.
Understanding the costs of holding inventory is key to creating a stocking plan that balances inventory costs and the stockout costs discussed in the first post of this Total Cost Optimization series.
Plan Instability Costs
Another key inventory cost is the cost of plan instability.
No inventory plan for service parts can be completely static, as business situations the plan is supporting change over time. New customers are added, new products are introduced, and products go out of support. Your network may need to evolve over time to support changing business needs. If you have technicians that hold inventory, technician turnover will also contribute to plan instability.
However, changes to a plan cost money. Each time a stocking plan changes, there are transportation expenses moving parts in your network to adjust to the new plan. If you use a 3PL, in addition to the transportation expense of moving a part, there are inbound and outbound charges as parts are moved from one stocking location to another.
Technicians that hold inventory are particularly sensitive to plan instability. If you send a technician a part for their van stock, and request that part be returned as excess, only to send it back again a short time later, technicians notice. Their time is wasted. Each change to their stock means they need to do some level of reorganization of their inventory.
A cost-optimized inventory plan will consider these operational expenses of changing a target stock level. Each stocking level change must provide more sufficient cost-benefit, in either reduced stockout cost risk or reduced inventory holding costs, to justify the operational costs driven by changing the stock level.
Summary
In this article, we discussed that there are organizational costs of holding inventory and operational costs to changing stock targets. In the final part of this series introducing Total Cost Optimization, we’ll discuss how when these inventory and instability costs are properly balanced with stockout costs, you will have achieved true optimization of your service parts inventory plan: The lowest possible operational costs of providing excellent service to your customers.
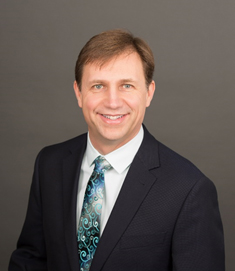
Mike Ross
Director of Product Strategy
Mike Ross is one of our primary subject matter experts. He has been on the Baxter Planning team since 2000, currently as Director of Product Strategy. Mike works on new feature conceptualization, requirements, and product design.
For more than 20 years Mike Ross has designed, developed, implemented, and supported off-the-shelf solutions for service parts planning that have been used at over 100 companies in a broad range of industries, including telecommunications, medical equipment, energy, imaging, printing, and aerospace. Mike has led many service-parts implementation and consulting projects and maintains solid client relationships focused on continuing education and process improvement. And in 2014, he was named as a Supply Chain “Pro to Know” by Supply and Demand Chain Executive magazine.
Mike lives in the Rochester, NY area with his wife and three amazing kids, as well as a dog, three fish, a leopard gecko, and a hedgehog. Mike and his wife enjoy running 5Ks (slowly) in their spare time.